Traditional techniques
Let us briefly introduce the long-established techniques and our careful works as craftsmen of Kyoto.
Hyogu are produced through a number of processes.
We’d like to raise your interest by looking at these processes which are rarely seen by the general public.
Gilding
You might have seen in a temple an altar, where the object of worship is placed, sparkling with gold color.
Gold was said to be used because its brilliant light would let you feel the Land of Happiness.
The color of gold may remind you of “pure gold,” but gold foil has a more calm and soft brilliance, which quiets your mind while shining.
I once encountered an awesome work of gold paper covering in a temple in Shimonoseki.
When I learned that it was a work by Sotaro Hashimoto, our 3rd President, 70 years ago, I felt happy and honored.
We’ve been receiving many orders from temples since the time of the 1st President, and the techniques of gilding have also been passed down since then.
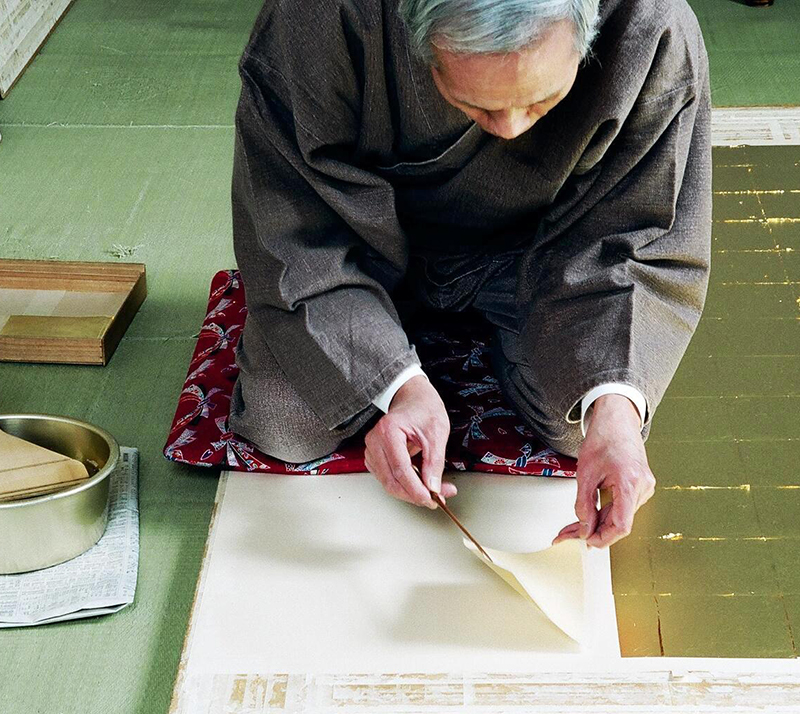
Gold paper Covering for Temples
Our biggest characteristic in conducting gold paper covering is that we can do both the manufacturing of authentic gold paper and covering on-site.
If manufacturing and covering are separated, the locus of responsibility can be unclear in the case of a problem.
Partly in order to avoid such problems, we conduct both manufacturing and covering.
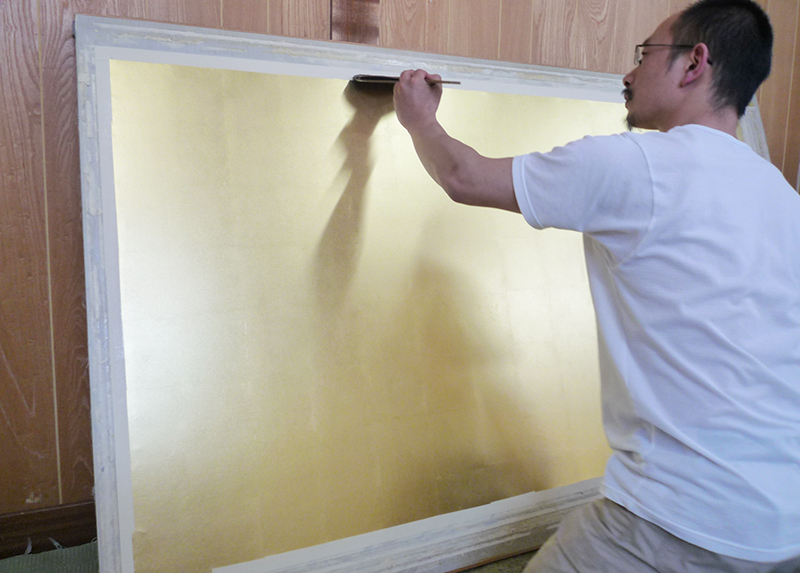
Tachikiri-type 157-millimeter-square authentic gold paper
We use entsuki type of authentic gold foil for authentic gold paper covering.
However, in light of recent economic concerns, it may be difficult for customers to useentsuki authentic gold paper.
We felt very sorry that some customers have given up using traditional gold paper gilded with authentic gold foil, and instead use industrially-made gold paper.
In order to resolve this, we developed large tachikiri gold foil.
While entsuki foil usually uses 128-millimeter-square foil, large tachikiri foil is a 157-millimeter square.
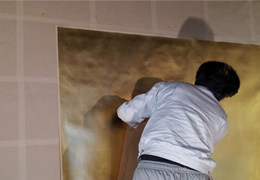
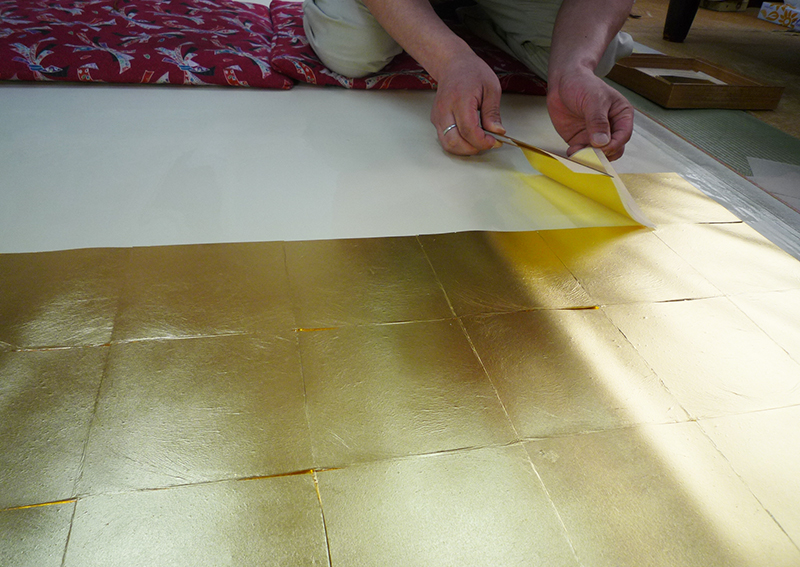
Materials used for authentic gold paper
We use truly selected materials for producing authentic gold paper.
Gold foil is purchased from Kanazawa.
We visit the gold-foil craftsman’s house to check in advance how the gold foil is manufactured and have preliminary discussions with them.
As for the torinoko paper used for the base of gilding, we also visit the paper factory in Echizen to check the manufacturing conditions and have preliminary discussions with them.
We will continue to make every effort to produce better products.
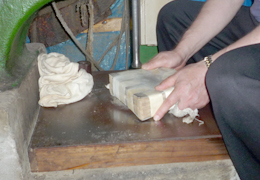
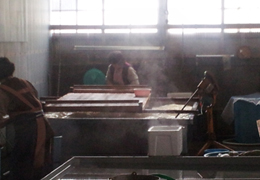
The flow of covering at the site

The above is the rough flow of the work in the case the base is plywood.
We also handle cases where the base material is unusual.
Typically, we recommend plywood for the base.
Processes of gilding
1. Drawing the lines
Draw the dimension lines for gilding on torinoko paper*1. This is the basis for all the processes, so make exact right angles in frame borders.
*1: Torinoko paper Soft and delicate gloss Japanese paper made using blended fibers of ganpi, mitsumata and other plants. Its faint yellow color is like the color of a chicken egg. Because it is durable and effectively reflects against ink, it is also used for Japanese paintings. We use hand-made torinoko paper specially selected by the manufacturer.
2. Board for drying
Paste on a board the torinoko paper with lines drawn. Place all the corners accurately according to the frame borders.
3. Base coating
After leaving the board until dried, apply the dosa liquid coat on the torinoko paper. Repeat the process of applying and drying at least seven times.
This process is easily affected by the weather, so the number of times should be decided carefully.
If you do it less, it would cause the gold foil to come off, and if you do it more, an unpleasant gloss would appear on the surface after gilding.
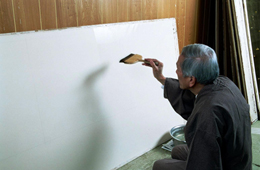
4. Applying oil
Apply some oil on foil paper using a tool called a baren.
If you apply less oil, it would come off the paper at the time of gilding, and if it’s too much, you can’t successfully peel off the foil paper at the time of gilding.
You have to be sensitive in deciding the amount of oil used.
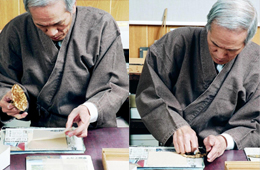
5. Peeling off the hakuaishi paper
Gently peel off the hakuaishi paper on the foil paper using bamboo tweezers.
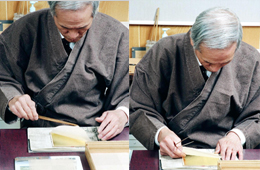
6. Attaching the foil paper to the foil
Smooth out the foil and attach the foil paper. When doing this, you need to be careful not to make wrinkles in the foil because they won’t go away when gilding. Subtle adjustment of strength is required.Gold foil*2 is as thin as 0.0001 mm, and easily blown off with soft breath.
*2 Gold foil There are two types of gold foil; entsuki and tachikiri. We use entsuki, because it has a calm brilliance and is very thin, making boundaries between pieces of foil less visible.
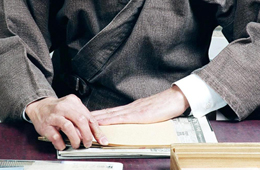
7. Gilding by transferring the foil
Apply the dosa liquid coat thinly on the torinoko paper that you have coated earlier.
Melt the coating of the torinoko paper. If the amount of dosa is too much, it goes to the surface of the foil, and if too little, the paper and foil wouldn’t be bonded.
Subtle timing is required for achieving adequate amount.
8. Mending and coating
After leaving the gilded gold paper until dried, wipe it with floss silk. Mend small holes, etc., on the foil. Pay the closest attention not to lay a piece of foil over another. After mending, wipe it with floss silk again. Finally apply dosa even more thinly than you’ve done at the time of gilding. This process aims at protecting the surface.
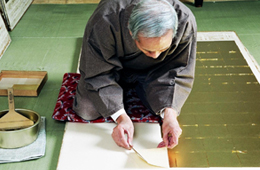
9. Checking the finished gold paper
Finish the work by carefully checking that there are no wrinkles, that no piece of foil is laid over another, and that there are no peelings.
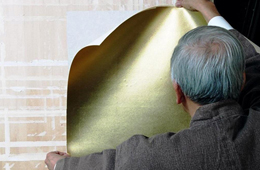